Today’s complex machine vision applications demand unconventional wavelength bands, combinations of visible and non-visible wavelengths like UV, NIR, or SWIR or exclusively require non-visible wavelengths. Multispectral machine vision cameras are well suited for meeting the increasing demands of diverse spectral capabilities, but they are often associated with high costs.
The key to cost-efficient and effective multispectral machine vision isn’t just in the cameras; it also includes illumination. In this blog, we will guide you through the successful implementation of highly efficient multispectral lighting for machine vision and multispectral imaging solutions.
Steps for Efficient Machine Vision Implementation
When it comes to multispectral imaging solutions and multispectral machine vision implementation, lighting often takes a backseat to camera setup. However, this oversight can prove costly. Opting for quality multispectral illumination solutions upfront not only saves costs but also enhances the overall efficiency and accuracy of machine vision systems. Here’s how to set up efficient multispectral machine vision systems-
1. Set Inspection Goals
Depending on the specific application, a multispectral machine vision system can inspect for defects, contaminants and irregularities in a sample. It is crucial to assess your machine vision application’s unique requirements. Consider factors such as the type of objects you’ll be inspecting, the environmental conditions, and the desired output. Take print inspection for example, if you are looking to detect any minute errors or imperfections within a printed work, RBG machine vision lighting is the best way to do it.
2. Estimate Inspection Time
When estimating inspection time, take into account the type of inspection needed. For some applications, inspection of the machine vision system cannot slow down the production line. LED technology provides greater opportunities to select specific wavelengths allowing more precise inspection or multiple inspections to be carried out at the same time. For example, a single COBRA MultiSpec LED line light configured with specific IR wavelengths as well as visible light can be utilized to inspect hazelnuts identifying dirt, stones, shells and other materials for removal, can all be completed in a single pass.
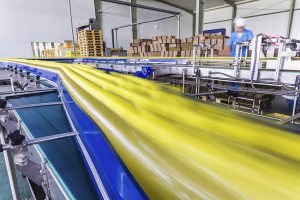
3. Define Features or Defects
Machine vision systems can be used for a wide range of inspection applications. In meat and fish inspection, for example, a machine vision system helps in identifying fat and water content, analyzing presence of bone or packaging or cuts and inspecting any potential damage. Clear specification of a defect for the object to be inspected is essential before investing in any of the hardware.
- What are the most common defects of the object?
- What features distinguish a good part from a bad part?
4. Select a Proper Lighting Source and Technique
Conduct an illumination study and choose a feature-appropriate light solution with suitable brightness and sufficient contrast that generates accurate and reproducible inspection results with good control of the environment. High quality illumination which allows seamless contrast optimization is critical to maximize inspection quality, speed and reliability.
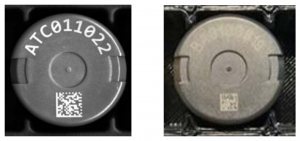
The most commonly used illumination techniques are back lighting, front lighting, diffuse lighting, bright field and dark field lighting. LED lighting is highly efficient in providing directional front lighting including bright field and dark field. Quite often, a simple re-positioning of the light source in relation to the camera can result in a far superior light- or dark-field image. Therefore, it is important to have a light source that is small, compact, and provides a greater degree of flexibility in terms of where it can be positioned within the larger machine vision system. For example, the narrow profile of the COBRA platform allows for the light source to be placed in an almost co-axial position to the camera. This flexibility in light vs camera orientation can be of significant benefit to the quality of image obtained.
Depending on the application, the uniformity and intensity of the LED source can be manipulated to get the best contrast. The use of chip-on-board LED technology allows us to achieve maximum light from as small a source as possible. Chip-on-board LEDs also allow for excellent spectral uniformity even when using multiple LEDs of different wavelengths.
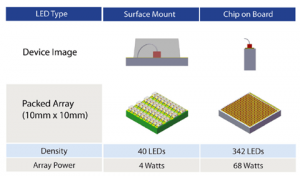
5. Find Proper Optics
After choosing the perfect LED lighting solution for your application, it is time to choose the optics to minimize line width and spectral uniformity. Depending on the application, this could be a specific lens position or diffuser type. Selective diffusers, such as the 30:1 diffuser for example, allows one to achieve a fully uniform spectrum along the line of the illumination, but without broadening the line width itself.
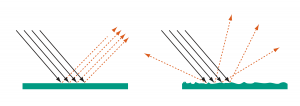
6. Choose a Camera
This depends on the positioning of the inspection/manufacturing process- whether it is in-line or off-line. An 8-bit analog camera offers a standard frame rate of 30 FPS, which has its own limitations. Choosing a light source that gives good illumination where the camera’s spectral response is highest reduces noise and results in a higher-quality image. LED technology is highly capable of boosting the spectrum which in turn compensates for any shortcomings in a camera’s response sensitivity.
7. Build a Prototype
Once optics are chosen, consider the environment to design the mechanical configuration. The mechanics of lighting solutions deal with not only how to hold and maintain relative positions between LEDs and optics, but also, how to protect the product from the environment and to provide thermal management. Since LEDs typically generate less heat than their halogen incumbents, for example, there can be significantly less demand on the cooling systems associated with the multispectral machine vision system.
8. Integrate all the Components
Choose image processing software and algorithms that complement the selected hardware. Additionally, pay attention to proper installation, calibration, and testing procedures. Ensure compatibility and integration between the multispectral lighting solution and cameras to maximize efficiency and cost savings.
9. Test and Calibrate
There are four main factors that influence production line speed and reliability in relation to lighting systems- light technology, processing time, downtime and changeover time. Proper installation and calibration are the keys to a successful multispectral machine vision system.
Setting Up the Multispectral System
Within machine vision systems, inappropriate or poor-quality lighting can often result in longer processing times and reduced throughput. We recommend developing the lighting solution early in the vision system design process.
Ensure Consistent Lighting Conditions
Consider the fundamentals of wavelength, angle of illumination and uniformity of the lighting system- wavelength, angle of illumination, uniformity, speed & reliability.
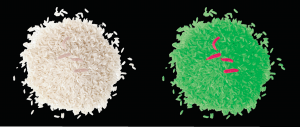
Because the product on production lines is moving, there are three solutions to ensure a good image is obtained. The first option is to stop the product. In some cases, this is not appropriate. The second option is to strobe the light source and as such freeze the motion. Strobing can be an extremely useful tool. If used correctly, it can offer increased intensity and longer illuminator lifetimes; however, if used incorrectly it can result in failure of the light or reduced lifetime. The third option is to utilize a line scan system which will take a continuous image of the production line. These vision systems are well-suited to inspections at higher speeds.
Budget Considerations and Cost Analysis
Utilization of LED-based machine vision systems should result in reduced costs, the elimination of subjective judgment, and allow production lines to run free of fatigue. When designing a machine vision system, it is important that the best solution should consider not only the up-front costs of the system, but also the lifetime costs in comparison to alternative solutions, as well as the measured impact on the business or research.
Identifying and Overcoming Potential Challenges
It is important to consider the potential challenges including physical constraints, object characteristics as well as ergonomics and safety aspects of the machine vision system. The size and shape of the machine vision workspace, lighting working distance, target object orientation (whether it is moving or stationery or indexed), light source positioning, potential light contamination, eye safety are some of the most common challenges.
- An LED multispectral machine vision system can be operated in either continuous mode or strobe mode. In strobe mode it is possible to achieve short periods of higher intensity, and by synchronizing sequential pulses of varying wavelengths, one can also obtain multispectral images using a simple monochrome camera.
- The use of halogen lighting, or even the presence of high levels of ambient lighting, can require the use of high- or low-band pass filters to remove unwanted wavelengths. However, by switching to a multispectral LED solution, and selecting only those wavelengths required, the need for filters could be completely eliminated; resulting in a simpler, more affordable, and safer multispectral machine vision system.
- Easy access to the machine vision system components allows for regular cleaning to get rid of any build up or dust that may hamper image quality and light intensity.
- Safety features can be integrated into the light through a blend of electronics, optics, and software, ensuring the Illuminator isn’t accidentally overdriven to avert potential catastrophic failure within the host system. ProPhotonix prioritizes safety within its designs, employing measures such as continuous thermal monitoring of substrate temperatures, flagged alarms controlled by software, and safe shutdown procedures.
Conclusion
While setting up machine vision cameras is relatively straightforward, the critical impact of lighting technology on system performance is frequently underestimated. Choosing the right lighting technologies can streamline processes, reduce errors, and minimize maintenance expenses, proving to be a smart investment.
ProPhotonix, committed to enhancing efficiency while prioritizing safety, integrates cutting-edge safety features into its multispectral LED illumination solutions. Our team of experts can guide you through the intricacies of selecting the most suitable lighting for your machine vision system, helping you achieve optimal results. We work in partnership with our customers understanding their specific application needs and supporting them through specification to completion of their multispectral machine vision systems. Explore further into our offerings encompassing multispectral imaging solutions and hyperspectral imaging solutions. Contact us and receive free professional advice now.
ProPhotonix is a leading designer and manufacturer of Laser Diodes, Laser Modules, UV LED Curing Systems, LED Products, and UVC LED Disinfection Systems. Contact us for free expert advice on selecting the optimal solution for your system.